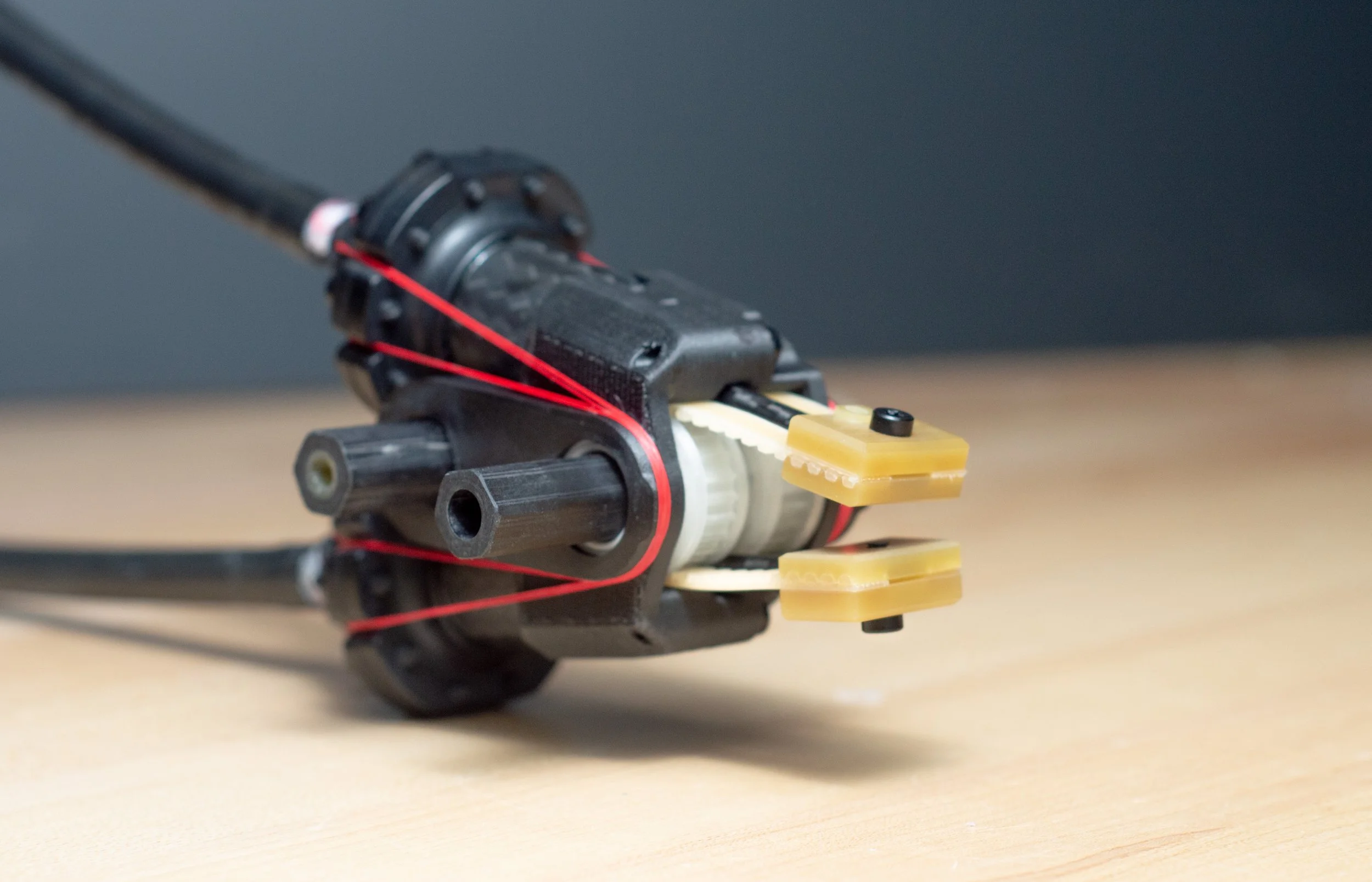
Hydrostatic Gripper for Low-Impedance Haptic Manipulation
This is the first project of my PhD research and has been used regularly since to conduct controls research in our lab, as well as for the key component of our Xprize avatar competition robot.
It is a 2 DOF hydrostatic gripper capable of haptic quality force feedback. The two fingers are coaxial, so each finger can have an individual actuator while achieving wrist rotation and grip opening. The gripper weighs 220g and has a grasp force slightly stronger than a human. The design goal was to make a low friction, haptic gripper for use on a commercial manipulator for conducting manipulation tasks requiring a sense of touch rather than just precise position control.
A great example of this is scooping up a piece of fish from a table; traditional grippers struggle to use contact with the table to scoop up an object.
The low-impedance of the fingers allows for very light, quick motion allows for dynamic performance such as catch a thrown object.
Below, the gripper in a hydrostatic configuration with actuators coupled to direct drive motors for control
Above, the low impedance transmission allows for the finger to be pressed against the surface, allowing it to scoop up a piece of raw fish. It is also fast enough to catch objects while teleoperated.
Below, a demonstration of the grip force (orange) while grasping memory foam and elastic foam. the curvature shows the relaxing of the memory foam of different densities.
Nonmetallic Hydrostatic Actuators
Nonmetallic actuators can be cheaply manufactured, resulting in widespread adoption of robotic systems, as well as use in corrosive or hazardous environments like nuclear disasters or underwater
Tensegrity Rotary Actuator
The geometry is designed to optimize load paths and allow the use of kevlar thread to take the tensile loads instead of bulking up parts and using more bolts. The plastic parts are better in compression, and the fiber wrap keeps them from taking tensile loads.
This actuator is being used to create a manipulator for an underwater ROV, for remote teleoperation and is funded by the US Navy.
I have developed a shaft and clamping system, using carbon fiber shafts I milled into a rounded hex profile for good torque transfer and clamping, while still allowing the use of standard bearings.
The entire actuator can be 3d printed or injection molded to bring down cost to under $100 each
Two of these actuators are combined to create a hydrostatic transmission that is extremely low friction and high torque density
A significant advantage of these actuators is the ability to remove the actuation power source, typically a large direct drive motor, from the mechanism or manipulator. This allows the mass and size of the motor to no longer be a constraint or negatively impact the
XPrize ANA Avatar Challenge Finals
Team Northeastern placed 3rd at the finals competition testing. A wireless robotic avatar was developed using the same concept we used for semifinals testing. Competition tasks included using a drill, social interaction, navigation, pick and evaluate and place, and using haptics to select a rough rock.
XPrize ANA Avatar Challenge Semifinals
We placed third in the semifinals as well, performing the tasks much faster than most teams with our very intuitive and simple yet capable system. Our team of six PhD students worked very hard to pull the system together in the weeks leading up to the competition. We had no idea what the competitors would be like, making it difficult to make design decisions.
We repurposed the gripper I had developed for use in the competition as a haptic teleoperation system. A second gripper was modified to be a user interface. I designed the input arm which used encoders to control the UR5, as well as the counterbalance system. Integrating all of the systems into one, fitting all the motors and power electronics together and within the requirements of the competition was a challenge.
The crew working the event was excited to try our system, and stayed late after the competition to demo it.
I used my years of coaching experience to inform user interface design decisions as well as conduct training of system operators, which had to perform tasks using the system after just one hour of training.
Manipulator for Low-Impedance, Haptic Manipulation
The target was to develop a platform for haptic manipulation research, in the lab and deep underwater. I developed nonmetallic hydraulic actuators, more about them below, which I used for this actuator. The wrist of the manipulator is modular, allowing reconfiguration for a desired task or based on user preference. The total moving mass of the manipulator is 1.13 Kg, 600g of which is the wrist. The payload of the manipulator is a minimum of 2 Kg. The goal of the design is to feel and use interaction forces to aid manipulation and perform tasks in a natural, compliant manor.
It uses a novel shoulder mechanism to locate the two shoulder degrees of freedom on the mechanical ground, and the elbow actuator grounded to the shoulder pan actuation.
The novel forearm is at an angle of 30 degrees to move the shoulder and elbow away from the line of sight of an operator or vision system on a mobile robot.
Other Projects
In addition to those primary projects, I have worked on a few other minor projects that did not get as far along due to prioritization of projects.
Linear Hydraulic Actuator Arm
I designed an arm using the same linear actuator as I used in the gripper and a new larger version.
The elbow mechanism is a linkage-differential I came up with. The linkage uses the larger, more powerful actuator for elbow flexion and extension. The wrist roll is achieved using the bevel gears and the smaller actuator. Since the moment arm for the wrist is significantly less, we use the smaller, weaker actuator.
Flying Bonnet, Fiber Hinge Actuator
In experimenting with different approaches to designing actuators using rolling diaphragm, I designed and prototyped an entirely 3d printed and kevlar thread actuator.
The actuator has the outer parts move and rotate an irregularly shaped pulley. Instead of bearings, the rotation is restrained by a kevlar threaded hinge. The output it connected directly to the flange of the pulley.
Ultimately we decided the approach was not further persuing and we put our efforts towardsother projectes rather that iterate and make the actuator more robust